
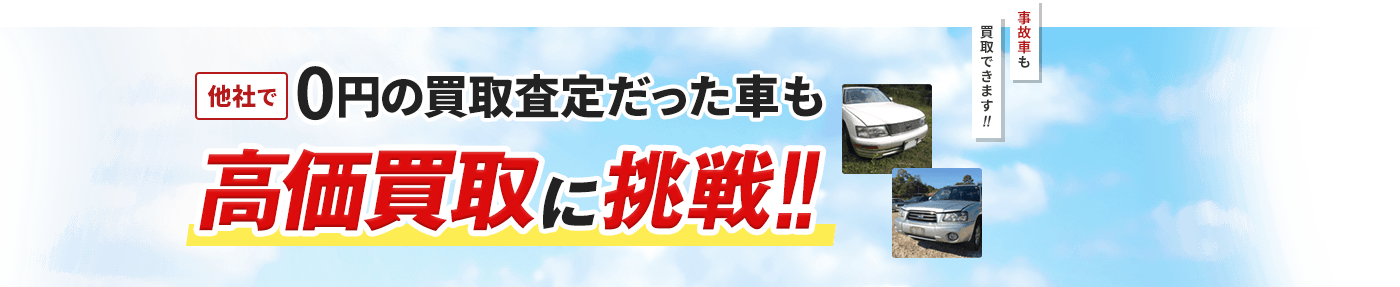
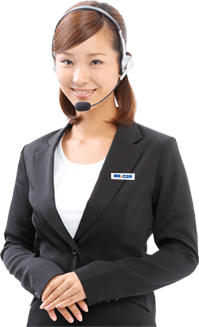
自動車のプラスチック化は、1973年の第一次オイルショックをきっかけに、省エネルギーのための軽量化などの理由から急速に進みました。
自動車は年々厳しくなる安全基準や排ガス規制、高機能化によって部品点数が増加する一方で、燃費や走行性能向上のためにさらなる軽量化が求められています。 各自動車メーカーは、自動車におけるプラスチックの使用割合をさらに増やそうとしています。
例えば、2014年12月に発売されたダイハツの「ムーヴ(LA150S/LA160S)」では、フロントフェンダーとバックドアに樹脂素材を採用しています。
ムーヴの樹脂製バックドア
今回は、自動車に使われているプラスチックの種類や要求される性能などについて書いていきたいと思います。
はじめに、プラスチックとは、どのような材料のことを言うのでしょうか? 日本工業規格(Japanese Industrial Standards)を確認すると、JIS-6900では 「高分子物質を主原料として人工的に有用な形状に形作られた固体である」 と、定義されています。 高分子物質とは一般的に分子量が一万以上ある物質のことです。
もともとプラスチックは、物の性質を表す言葉でした。 英語では「可塑性(かそせい)」という意味があります。対義語はエラスティック「弾性」です。
可塑性とは、外から力を加えることによって形を変えることができ、加えた力を取り除いても形がそのまま残るという性質のことです、 逆に弾性とは外から力を加えることによって形を変えることができ、加えた力を取り除くと元の形に戻ろうとする性質のことです。
プラスチックは、加熱すると柔らかくなり、任意の形に変えられる可塑性(plasticity)を持っているのでプラスチックと呼ばれています。
一般的にプラスチックは、合成樹脂と同じ意味のように使われていますが、定義的には「樹脂」は原料であり、「プラスチック」は成形品を指しています。 プラスチックは、主に「熱可塑性樹脂」と「熱硬化性樹脂」の二つのタイプに分けられます。
「熱可塑性樹脂はチョコレート型」 「熱硬化性樹脂はクッキー型」 と例えられることがあります。
熱可塑性樹脂は、チョコレートのように加熱すると柔らかくなり、冷やすと固まる性質の樹脂のことを言います。 熱硬化性樹脂は、クッキーのように、いくつかの原料を混ぜ、加熱すると固くなる性質の樹脂のことを言います。
この二つの樹脂を、使用する場所や要求される性能によって使い分けています。
熱可塑性プラスチックの種類は一般的に
・汎用プラスチック
・汎用エンジニアリングプラスチック
・スーパーエンジニアリングプラスチック
に分けることができます。
汎用プラスチックは主に
・ポリエチレン(PE)
・ポリプロピレン(PP)
・ポリスチレン(PS)
・ポリ塩化ビニル(PVC)
・ABS樹脂(ABS)
などがあります。
工業用部品に主として使用されるプラスチックを、エンジニアリングプラスチックといいます。s
その中でも主要に使用されている5種類
・ポリアミド(PA)
・ポリアセタール(POM)
・ポリカーボネート(PC)
・変性ポリフェニレンエーテル(m-PPE)
・ポリエステル(PEs)
を一般に汎用5大エンプラと言います。
エンジニアリングプラスチックは、一般に耐熱温度が100℃以上で、強度500kgf/cm2未満・曲げ弾性率24000kg/cm2のプラスチックのことを言い、これ以上の高性能な樹脂はスーパーエンジニアリングプラスチックと言います。
マークXの樹脂製フロントバンパー
自動車にプラスチックを使用することによって、どんなメリットがあるのでしょうか?
・軽量化
軽量化については言うまでもありませんが、金属が用いられていたパーツをプラスチックに置き換えることにより、軽量化、それによる燃費の向上が期待できます。
・デザイン性の向上
昨今の自動車は、角ばったデザインからなめらかなフォルムへと変貌しつつあります。
金属では成形が難しい複雑な形状でも、プラスチックなら容易に成形(射出成形など)することが可能です。
・復元性
これは主にボディ外板に言えることです。
樹脂製のバンパーの場合、少しぶつけた程度ではへこんでも、元の形に戻るという点でメリットがあります。
・防錆
金属の敵、それは錆びです。
錆を防ぐため、自動車に使われている金属には特殊な塗料を下塗りするなど、防錆が施されています。
その一方でプラスチックは錆びないので防錆加工が必要ありません。
・防振、防音効果
ボンネットやドアの内張り、これには、外観を美しく見せるだけではなく、防振、防音効果があります。
自動車の内張りをすべてはがしてしまったら、車の中がエンジン音やロードノイズで騒がしくなるのは想像に難くないですね。
20系プリウスの樹脂製バンパーとインナー
次に、様々な環境下で使用される自動車ですが、自動車に使用されるプラスチックにはどんな性能が要求されるのかについて挙げていきます。
・耐衝撃性
近年、さらに高まる自動車への安全性の要求から、特にバンパーなどは、高い耐衝撃性が求められています。
・耐候性
自動車は、日光や降雨、高温や高湿など過酷な環境に置かれることが多く、特に外装部品では、高い耐候性が要求されます。
・接着性
プラスチックを使用したときのデメリットの一つが「塗料のノリ」が悪いものがあります。
外装など、塗料を塗る必要があるパーツには、接着性の高い材料を使用する必要があります。
・見栄え
近年増えている、押し出しの強いデザインの車にはメッキパーツが多用されています。
メッキ加工ができる樹脂の種類は限られているので、それを考えた材料選びが必要です。
また、塗料を使用しない場合、材料そのものの発色や光沢も考慮される必要があります。
・高剛性
自動車は、走行中の路面の荒れや段差など絶えず負荷がかかりひずんでいます。
高剛性のパーツを使用すれば、走行中のきしみ音などを低減することができます。
自動車は、実に様々なパーツが、集まってできています。 上に示すようにそれぞれのパーツで要求される性能がちがい、適材適所にプラスチックを使い分ける必要があります。
では、実際にどのパーツにどんなプラスチックが使用されているのか、いくつか例を挙げて詳しく見ていきます。
・バンパー
自動車に使用されている樹脂部品として、初めに思い浮かぶものはバンパーではないでしょうか。
バンパーに求められる性能は、耐衝撃性や耐候性です。
バンパーには、耐衝撃性に優れた変性ポリプロピレンが主に採用されています。
PPは、耐候性が低いため、塗装をされた状態で使用されています。
バンパーの中に、発泡ポリウレタンなどの発泡体を組み込んで高衝撃に対応しているものもあります。
・ヘッドライト
ヘッドライトに求められるのは、何と言っても光を通す透明な材料であることです。
さらに割れにくい高い強度が必要とされます。
よって、非結晶性プラスチックで、高強度なポリカーボネートが使用されています。
自動車のヘッドライト
・ホイールキャップ
ホイールキャップには、複雑な形状に対応する成形性、ブレーキの放熱に耐えうる耐熱性、塗装性が要求されています。
主に、PCやABSを混合させたポリマーアロイなどが使用されています。
自動車のホイールキャップ
・ホイールキャップ
ホイールキャップには、複雑な形状に対応する成形性、ブレーキの放熱に耐えうる耐熱性、塗装性が要求されています。
主に、PCやABSを混合させたポリマーアロイなどが使用されています。
・インパネ
内装のインパネ(インストルメントパネル)には、芯材、基材、表皮材など、様々な材料が使い分けられています。
芯材には高剛性のGFRP(ガラス繊維強化プラスチック)、芯材を覆う基材には、耐衝撃性に優れるABS樹脂や変性PPE、質感が求められる表皮材には、軟質ポリ塩化ビニルなどが使用されています。
・シート
シートには、表皮材、クッション材にプラスチックが使用されています。
表皮材にはPETでできた繊維や、ポリ塩化ビニル製の人工皮革が使用されています。
クッション材には、ポリウレタン系の材料が使用されています。
・エンジン周り
エンジン周りには、燃料や排気、吸気を送る配管(マニホールド)、電装部品などがあります。
使用される環境が高温であることや、高い信頼性が求められること、燃料やエンジンオイルに触れる場所であることから、ほかの場所と比べてプラスチックの使用される割合は低くなっています。
エンジン周辺では、騒音の低減や装飾のためのエンジンカバーに、PAが使用されています。
また、燃料タンクには主に耐食性、耐衝撃性といった観点から高密度ポリエチレンが使用されています。
自動車のエンジンカバー
・ホイールキャップ
ホイールキャップには、複雑な形状に対応する成形性、ブレーキの放熱に耐えうる耐熱性、塗装性が要求されています。
主に、PCやABSを混合させたポリマーアロイなどが使用されています。
続いて、自動車業界に進出しつつあるCFRP(炭素繊維強化プラスチック)についてです。 以前のコラム“自動車業界に導入されていく「CFRP」”でも書かれています。
CFRP(炭素繊維強化プラスチック)とはその名の通り炭素繊維で強化されたプラスチックのことをいいます。 主に母材にはエポキシ樹脂が使用されています。 軽量かつ高強度、高弾性といった特徴から、航空機やF1 カーでは、幅広く使用されています。
CFRPには、上にあげたような特徴がありますが、コストや手間がかかる、修理しづらいといった面から、量産型自動車では、まだ普及が進んでいません。 近年、自動車業界で注目されているのが、母材に熱可塑性樹脂を用いた「CFRTP」です。
CFRTPは、主に、不連続繊維を強化材として使用し、今までのCFRPに比べ、成形サイクルが短い、リサイクル性が良い、安価である、製造時のエネルギーが少ないなどのメリットがあります。 しかし、CFRPに比べ力学特性が劣る、材料自体にばらつきがあり扱いが難しいなどのデメリットがあり、各メーカーは開発にしのぎを削っています。
プラスチックは主に以下の3つのリサイクル法に分けられます
・マテリアルリサイクル
廃プラスチックをプラスチックのまま原料として新しい製品を作る
・ケミカルリサイクル
廃プラスチックに熱や圧力を加えて、プラスチックを合成する原料に戻してから再利用する
・サーマルリサイクル
廃プラスチックから熱エネルギーを回収して利用する。
>PP+E/P-T20< の、Tはタレク比率を表す
自動車に使われるプラスチック材料は、GFRPにはガラス繊維が添加されています。 バンパーなどの樹脂製品のPPにもタルクや塗料など様々なものが添加されています。 それらの添加がリサイクルへの障壁のひとつとなっています。
また、樹脂の種類が多いこと、同一の樹脂でも用途や成型方法によってさまざまなグレードにわかれているということから分別が難しくリサイクルが困難になっています。 一例として、PPにタレクを混ぜる理由は強度を出すためです。 しかし多くのタレクを混ぜると、強度が出る代わりにプラスチック材料が割れやすくなります。
そして強度が違うので製品用途によって、タレクの混合比率が異なります。 つまり同じメーカーでも車種や使用部分によってタレク混合比率が異なるので、リサイクルする時には、分別が非常に困難となります。
これらの要因から、現在、自動車の廃プラスチックのリサイクルは、直接燃やして熱エネルギーを取り出すサーマルリサイクルがメインとなっています。 しかし、環境負荷の低減といった観点から、マテリアルリサイクルやケミカルリサイクルの技術開発を進め、将来的には、これら3つのリサイクル方法から、コストや環境負荷が少ない方法を適切に選んでいく必要があると言えます。
近年の、自動車の燃費向上や走行性能向上のために軽量化が求められており、プラスチックの使用割合は年々上昇している。 自動車には様々な種類のプラスチックが適材適所で使われており、航空機やスーパーカーなど、一部の使用に限られていたCFRPも量産車に使われ始めている。
プラスチックの使用割合が増える一方で、リサイクルにはまだまだ課題が多く、これから更なる技術開発が必要であるといえる。 以上、最後までお読みいただきありがとうございました。
(執筆:岐阜大学自動車部)